Vaccine Delivery
Scheduling And Receiving Deliveries
This is the first and most vital step in a facility's vaccine inventory management system. As such, facility staff must be educated on how crucial this step is to the facility's ability to provide vaccines for patients, and this education should cover the following:
- Notifying the vaccine/pharmacy coordinator when new vaccines arrive from storage facilities.
- Ensuring that vaccine shipping containers are not left unpacked or unattended. If vaccines and diluents get too warm, their genetic material can become damaged—the vaccines now spoiled and unsafe. Thus, fresh vaccine deliveries must be attended to as soon as they arrive.
- Checking and ensuring proper vaccine storage upon arrival
Procedure for Unpacking Vaccine Deliveries
- Carefully unpack and store vaccines and diluents at recommended temperatures and document them immediately after they arrive. Newer technologies such as MRNA vaccines or subunit vaccines are especially sensitive to temperature changes and need to be handled with both care and speed.
- Ensure you do not place an unopened and/or unpacked shipment box in a vaccine storage unit. Vaccines are usually shipped with cool packs, and they may make the packaged vaccines too cold if they are not removed before placing the vaccines in storage units.
- Examine shipments for signs of damage and check that you are receiving the right vaccine types and quantities. This includes checking the following:
- The shipping container and vaccines for signs of physical damage
- The contents against the packing list to ensure a match. Note that the packing list for frozen vaccines will also show the maximum time vaccines can be in transit based on the shipment date.
- If you have lyophilized vaccines in your shipment, check that they come with the correct type and quantity of diluents.
- Check vaccine and diluent expiration dates to ensure they are not expired or near expiration.
- Check whether the shipment came with a cold chain monitor (CCM). If yes, check the log for any temperature excursion events during transit.
Vaccine Inventory Accounting
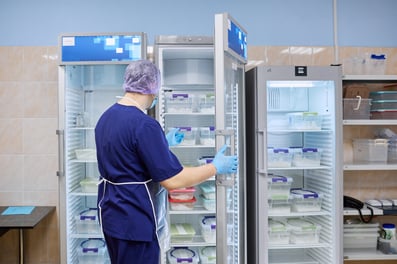
You will need a stock record to account for and document your vaccine inventory. Stock records help determine the type and amount of vaccine your facility should stock to meet patient needs. They also help you keep track of your inventory. You can keep stock records in either paper or electronic forms, and they should be updated weekly to include information such as:
- The date of delivery and initials of the person who unpacked the box
- The vaccine and diluent name and manufacturer
- The number and expiration date for each lot
- The number of doses received
- The condition of each vaccine and diluent upon arrival
- The CCM reading, if included in the shipping container
- The number of doses used
- The number of doses remaining
At least once a month, and before placing any vaccine order, count all vaccine and diluent doses and ensure that the number of doses in storage matches the documented doses in the stock record. Furthermore, always check expiration dates while counting vaccine stock and remove any expired doses immediately.
This is crucial as unique vaccine delivery methods and technologies like:
- Conjugate Vaccines
- Viral Vector Vaccines
- Live Attenuated Vaccines
- Toxoid Vaccines
- And Inactivated Vaccines
Additionally, you may want to use tally sheets to keep your stock records up to date. Including any additional doses or booster doses received.
You can place the tally sheets outside the storage unit door, or any other easily accessible location and have staff use tick marks to record every dose removed from the unit.
Vaccine Ordering
When ordering vaccines, it is best to order and stock only enough to meet patient needs because storing vaccines in surplus of your facility needs can expose you to the risk of waste and losses for the cost of goods sold. However, any existing supply chain restraints may make over ordering slightly a smart move.
In addition, the vaccines may expire before they can be used or compromised in some way. Thus, it is best to make fresh orders after checking your stock count.
However, note that while vaccine orders typically arrive within one or two weeks, there can be delays. Thus, it is best to factor that in when ordering your vaccines and avoid placing last-minute or rush orders. The CDC recommends reordering vaccine stock when you are down to about four weeks' worth of inventory.
Vaccine Stock Arranging, Rotation, and Removal
Your facility's vaccine coordinator or any other designated staff should rotate vaccine and diluent stock at least once weekly, and every time you receive a fresh vaccine delivery. Arrange the stock for each vaccine type so that doses with the earliest expiration dates come before those with later dates. This will ensure that you use up vaccines that are expiring sooner first. Also, ensure that expired vaccines are removed immediately after they are discovered to avoid accidently providing them to patients.
Vaccine Disposal
There are different reasons why you may want to dispose of your vaccines. Below we’ll briefly guide you in disposing of vaccines for common scenarios.
How to Handle Expired or Compromised Vaccines
You will need to contact your immunization program or vaccine manufacturer for specific information.
However, you may sometimes be able to return unused vaccine and diluent doses, unopened vials, expired vials, and potentially compromised vaccines for credit, even if they must be discarded.
- Open and broken vials and syringes, manufacturer filled syringes that have been activated, and vaccines pre-drawn by providers
As they cannot be returned, you’ll generally need to discard them per your state requirements.
- Empty vaccine vials
Most empty vaccine vials are not considered hazardous or pharmaceutical waste and do not require disposal in a medical waste container. However, you should check and comply with your state's requirements for disposal.
Protecting Vaccine Inventory with a Backup Power Solution
Medi-Product’s entire line of plug and play battery powered backup generators are line-interactive, enabling them to monitor power input and automatically engage when an outage occurs. When not being used, they can automatically charge their batteries
However, as soon as the battery system senses a loss of utility power, it switches to its batteries and keeps your machine powered in milliseconds. This means almost all equipment will continue to run as if nothing happened.
Furthermore, our systems are custom-sized to meet desired runtimes and support specific appliances as requested. Common requests include systems that can power entire procedure rooms or ultrasound labs for 8, 12, 24, and even 48-hours with one single system that all appliances can plug directly into.
And with three separate form factors to choose from, a MediProducts battery backup is sure to fit anywhere inside your facility whether you need:
- A standalone Plug-and-Play solution in the same room as your medical equipment,
- A Portable power station that can be moved around the room or your facility
- Or, a backup power system that remotely supplies power to the outlets your appliances are connected to.
Ensuring that no matter your needs the proper solution can be easily found.
All you need to do is contact us, and one of our product experts can quickly and easily design exactly what you need.